Georgia-Pacific Invests $18 Million into Camden Plywood Plant
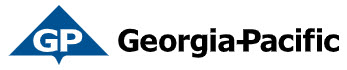
It was in the late 1800s when the small community of Camden, Texas, welcomed its first forest products mill. What began as the W.T. Carter Lumber Company is today one of Georgia-Pacific’s largest plywood operations. As one of the top plywood facilities in the South, Camden Plywood not only produces quality building materials for its customers, but also provides good solid jobs for east Texans. To ensure its longevity for years to come, Georgia-Pacific is embarking on a $18 million upgrade that will modernize the plant and help increase efficiency.
The capital improvement plan will focus on three different projects beginning with the plant’s dryer. “We’re rebuilding our dryer, which is more than 40 years old,” said George Standley, Camden Plywood Plant Manager. “The dryer is the heart and soul of plywood operations and is one of the most important stages of production. Controlling veneer’s moisture content is critical to producing a quality product.” The dryer project is scheduled to be completed in July.
While the dryer is being reconditioned, Camden Plywood will also undergo a project to modernize its stenciling and strapping operation. Currently performed manually, this job will soon be automated as the plant introduces a robotic strapping and stenciling system. “This area of operation can sometimes slow down the process since an operator has to manually place a stencil on a bundle of plywood, paint it and remove the stencil. This process must be performed several times to ensure that all the required markings are captured clearly,” said Standley. “The new automated strapper and stenciling system will increase efficiency.” The innovative technology is currently being installed.
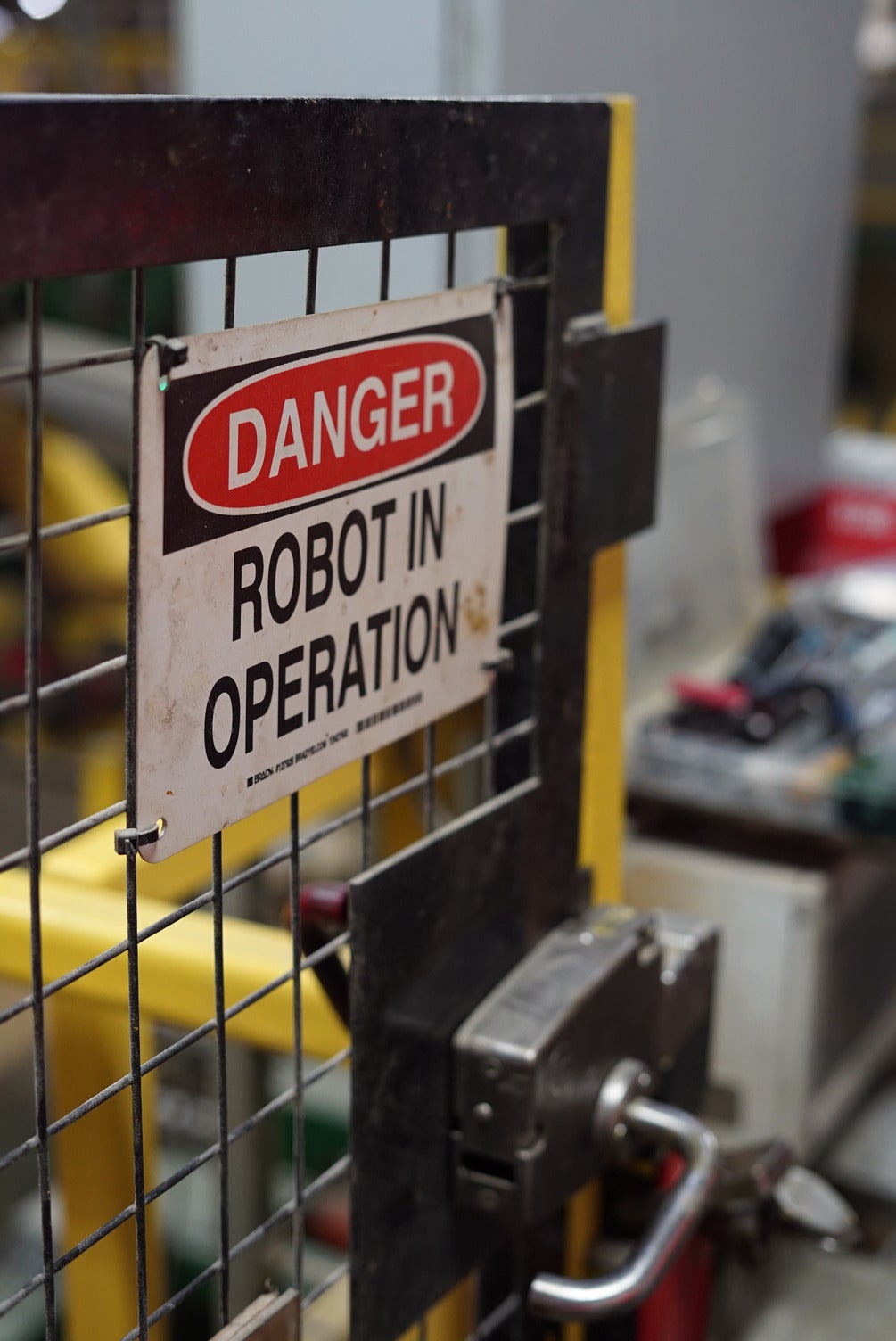
Later this summer, Camden Plywood will wrap up its capital improvement projects with the introduction of its robotic patch system. These robots are designed to detect and repair imperfections in wood veneer during production. Currently patching veneer is handled by multiple workers who are stationed on the line determining where the glue-like filler is needed and manually using it to repair the wood panels. According to Standley, the innovative technology will be operated by four robotic technicians who are now being trained on the system.
“Camden Plywood is an example of how plants are being modernized to not only improve production, but to attract, retain and challenge industry employees,” said Standley. “Modern technology can challenge employees and give them the opportunity to grow their careers. By adding robots to our lines, it is our goal to provide more meaningful work which leads to greater job satisfaction.”
Georgia-Pacific’s Camden Plywood facility employs approximately 500 people and over the next few months more than 100 contractors will be onsite performing the upgrades.
Source: Georgia-Pacific, LLC